齒輪生產(chǎn)中,合格率與一致性的差距往往源于淬火熱處理工藝的選擇。許多高合格率廠家的 “秘密”,正是用高頻淬火設(shè)備替代傳統(tǒng)火焰煤炭爐 —— 這不僅是技術(shù)升級,更是對齒輪性能穩(wěn)定性的根本保障,其差距體現(xiàn)在加熱精度、工藝可控性與質(zhì)量穩(wěn)定性的全方位碾壓。
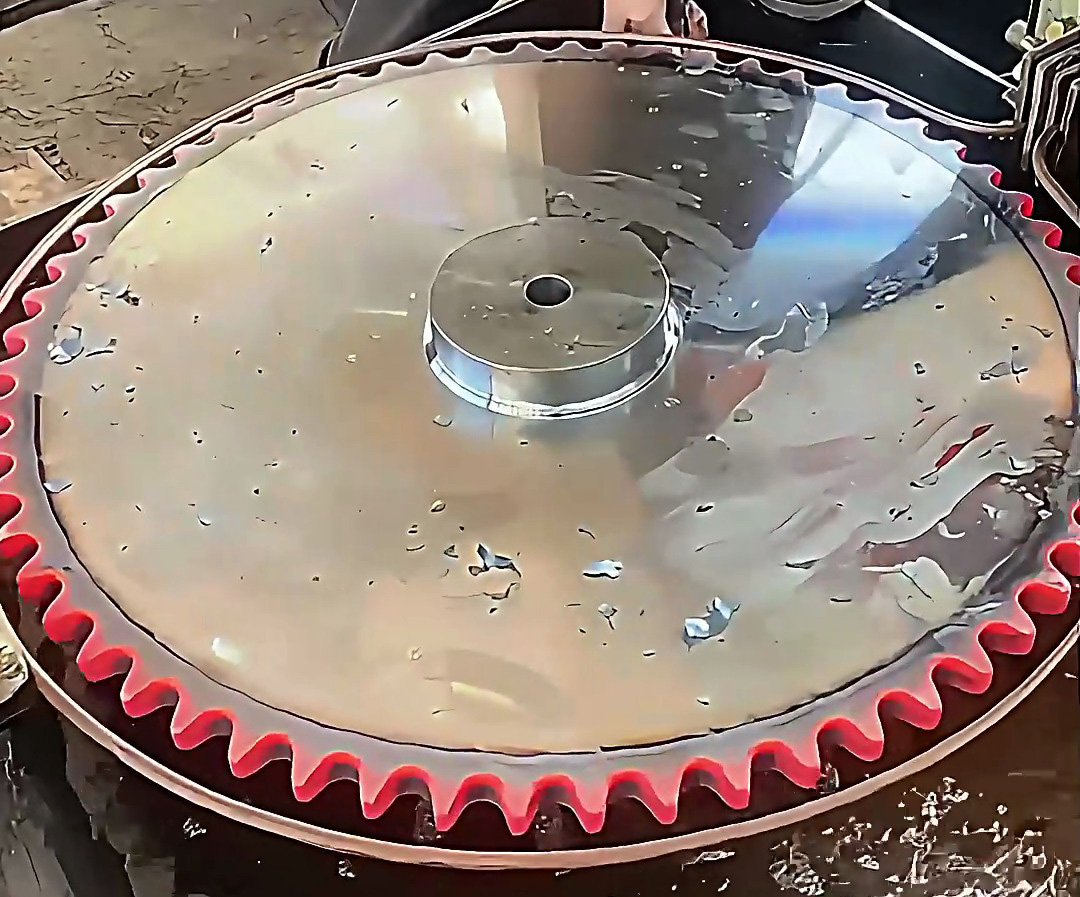
火焰煤炭爐(以焦炭、煤為燃料)通過明火直接加熱齒輪,其原理決定了難以克服的短板,直接拉低合格率:
加熱均勻性極差:煤炭燃燒的火焰溫度分布混亂(中心區(qū)可達 1000℃,邊緣區(qū)僅 600℃),齒輪不同部位受熱不均,同一齒輪的齒面硬度差常達 ±8-10HRC(合格標準需≤±2HRC);
溫度無法量化:依賴工人肉眼觀察 “鋼材顏色” 判斷溫度(如 “櫻桃紅” 對應(yīng) 800℃),誤差可達 ±100℃,導(dǎo)致部分齒過熱(晶粒粗大、韌性驟降)或欠熱(硬度不足、耐磨性差);
冷卻時機滯后:從爐膛取出齒輪到噴水冷卻的過程中,溫度會自然下降 100-200℃,奧氏體化不充分,最終硬度達標率僅 70%-80%。
火焰煤炭爐燃燒時產(chǎn)生大量 CO?、H?O 和煙塵,齒輪在高溫下會發(fā)生:
某小廠數(shù)據(jù)顯示:火焰淬火的齒輪,因氧化脫碳導(dǎo)致的早期失效占比達 30%,而高頻淬火可降至 1% 以下。
煤炭質(zhì)量(熱值波動)、爐溫分布(每次添煤后溫度驟升)、工人操作習(xí)慣(不同班次判斷標準不同)等因素,導(dǎo)致同一批次齒輪的性能差異極大:
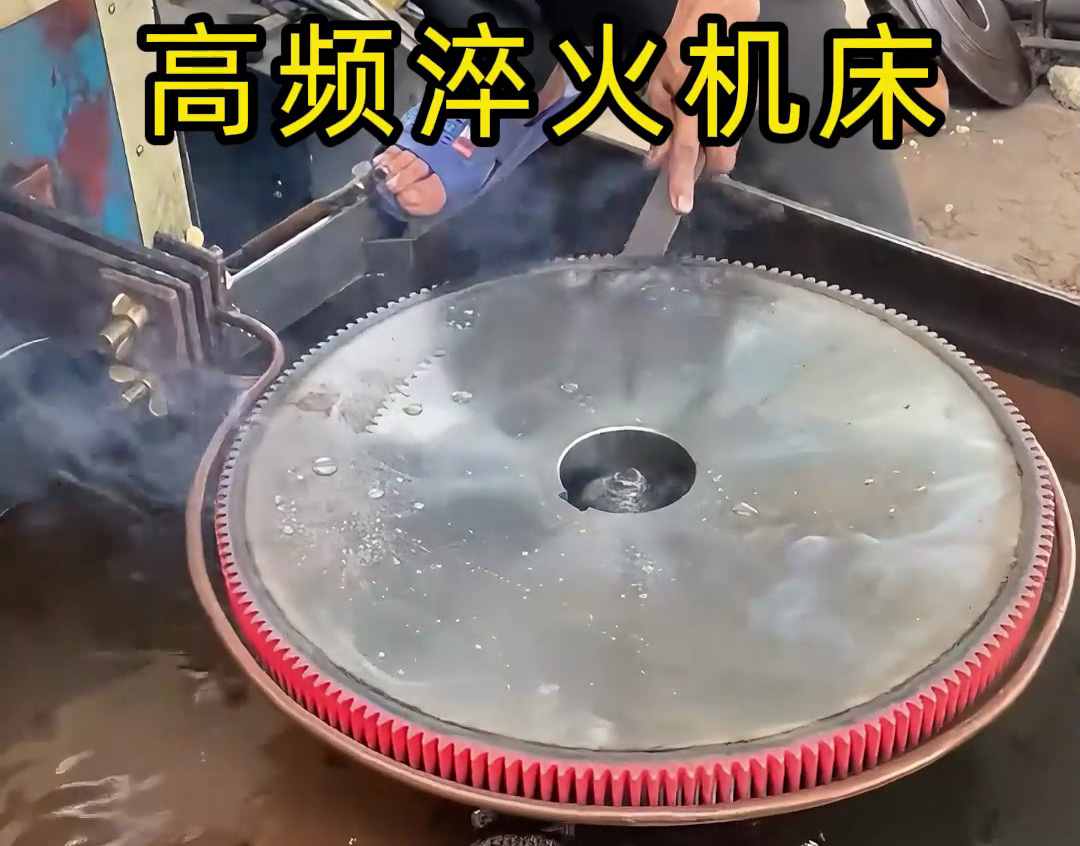
高頻淬火(頻率 30-100kHz)通過 “電磁感應(yīng)加熱 + 精準控溫”,從根源上解決火焰爐的缺陷:
局部定向加熱:定制化感應(yīng)線圈貼合齒輪齒面,僅加熱需淬火區(qū)域(齒面、齒根),非淬火區(qū)溫度≤300℃,避免整體過熱;
數(shù)字化控溫:通過 PLC 程序設(shè)定加熱溫度(如 860±5℃),紅外測溫實時反饋,功率自動調(diào)節(jié)(響應(yīng)時間≤0.1 秒),同一齒輪各齒溫度差≤±5℃;
微秒級冷卻控制:加熱完成后 0.5 秒內(nèi)自動啟動噴霧冷卻(壓力恒定 0.3MPa),確保馬氏體轉(zhuǎn)變充分,硬度偏差可控制在 ±1HRC 內(nèi)。
高頻加熱時齒輪不與明火接觸,且可通入惰性氣體(如氮氣)保護,實現(xiàn):
高頻淬火的參數(shù)(功率、時間、冷卻壓力)可存儲為程序,換班或換批次時直接調(diào)用,確保:

高頻淬火設(shè)備的初期投入(10-30 萬元)高于火焰爐(1-2 萬元),但長期收益顯著:
廢品率降低:按年產(chǎn) 10 萬件齒輪計算,高頻淬火可減少 2 萬件廢品(每件成本 50 元),年節(jié)省 100 萬元;
壽命延長:高頻淬火齒輪的疲勞壽命是火焰淬火的 2-3 倍,客戶退貨率降低 90%,品牌口碑提升;
人工成本下降:1 人可操作 3 臺高頻設(shè)備,替代 5-6 名火焰爐工人(需添煤、看火、搬運),年省人工費 20-30 萬元。
齒輪合格率與一致性的差距,本質(zhì)是 “可控工藝” 與 “經(jīng)驗依賴” 的較量。高頻淬火設(shè)備通過數(shù)字化、精準化的加熱方式,將齒輪熱處理從 “看天吃飯” 變?yōu)?“精準可控”—— 這就是優(yōu)秀廠家不愿外傳的 “秘密”。對于追求質(zhì)量的齒輪廠而言,升級高頻淬火不是 “選擇”,而是 “生存必需”,畢竟在精密制造領(lǐng)域,“差不多” 的產(chǎn)品最終會被 “差很多” 的市場淘汰。